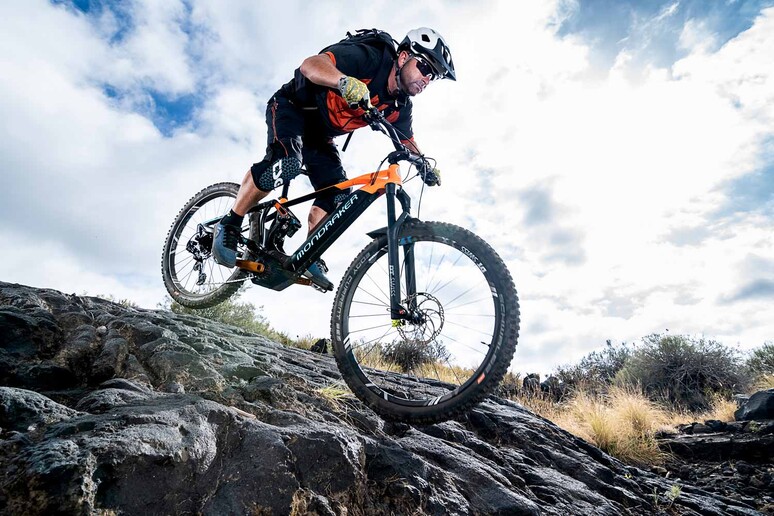
Fallbeispiel Bohle: Bestandsoptimierung in der Supply Chain
Die Marke „Schwalbe“ steht bei Fahrradfreunden für höchste Qualität. Das Bestandsmanagement der Ralf Bohle GmbH rollt nun ebenso rund - bei der Bestandsoptimierung hilft eine neue Software.
Die Marke „Schwalbe“ steht bei Fahrradfreunden für höchste Qualität. Das Bestandsmanagement der Ralf Bohle GmbH rollt nun ebenso rund - bei der Bestandsoptimierung hilft eine neue Software.
Grundlegende Veränderungen in Supply Chain und IT-Landschaft
Zwei neue Zentrallager in Asien dienen dem Vorstau
ERP- und WMS-System gleichzeitig ausgetauscht
Der Tire Tracker verfolgt Sendungen um die ganze Welt
WMS hat sich in der Lagerpraxis bewährt
Masterbarcode ist der Schlüssel zur Rückverfolgbarkeit
Termin gehalten, Ziele erreicht
Forschung und Entwicklung in Deutschland, Produktion in Asien, Lager für 3.500 Produkte in Asien und Europa, Kunden in 69 Ländern auf allen Kontinenten: In der Wertschöpfungs- und Lieferkette des Familienunternehmens Ralf Bohle GmbH mit Sitz im Oberbergischen Reichshof gibt es an Komplexität wahrlich keinen Mangel.
Zumal die Ansprüche der Kunden hoch sind. Fahrradhersteller sowie Groß- und Einzelhändler erwarten von den etablierten Marken „Schwalbe“ und „Impac“ nicht nur hohe Qualität, sondern eine entsprechende Lieferfähigkeit und Performance. Dabei spielt das Bestandsmanagement und Bestandsoptimierung eine zentrale Rolle.
Um diesen Kundenanforderungen weiterhin effizient und zu besten Kosten gerecht zu werden, beschlossen die Verantwortlichen bei Bohle im Jahr 2016 grundlegende Veränderungen – sowohl in der physischen Logistik als auch in der IT-Landschaft. Beides ist eng miteinander verknüpft und beeinflusst das Bestandsmanagement und Bestandsoptimierung.
Vor der Umstellung, die nach intensiven Vorarbeiten in verschiedenen Projektteams in 2018 abgeschlossen wurde, war der Lieferprozess folgendermaßen organisiert: Vier Bohle-Gesellschaften platzierten ihre Bestellungen unabhängig voneinander beim Produktionspartner, dem koreanischen Familienunternehmen Hung-A.
Optimierte Prozesse in internationalen Lieferketten – von der Bestellung bis zur Auslieferung. Inklusive Laderampenplanung, Integration Ihrer Transportdienstleister, Versandprozesse, Fracht- und Logistikkostenmanagement sowie Lagerverwaltung.
Seit der Neustrukturierung liefert der Produktionspartner in zwei Zentralläger in Indonesien und Vietnam, die von Logistikdienstleistern betrieben werden. „In diesen Lägern findet der Vorstau statt. Sie dienen als Nachschub für alle anderen Läger. Gleichzeitig werden viele große Kunden direkt von dort beliefert“, erklärt André Bösinghaus, Head of Logistics bei der Ralf Bohle GmbH.
Bohle entschied sich zu einer Aufstockung der weltweiten Lagerkapazitäten von 26.200 Paletten-Plätzen auf heute 44.000. Grund für das Investment: Dem Produktionspartner sollte eine Optimierung der Losgrößen in der Herstellung ermöglicht werden, ohne dass Bohle an Lieferfähigkeit einbüßt. Ein Zugewinn für das gesamte Bestandsmanagement.
Gleichzeitig setzte das Traditionsunternehmen auf eine Optimierung der Liefer- und Bestellprozesse. Dazu investierte der Fahrradreifenspezialist weiter in das Bestandsmanagement. Das gesamte ERP-System wurde ausgetauscht – und in Folge dessen auch das Warehouse Management System.
Besonders wichtig war es laut Bösinghaus, die bisher nicht koordinierten Bestellungen der vier Bohle-Gesellschaften zu konsolidieren. „Wir haben eine „Headquarter-Ebene“ in den Bestellprozess eingezogen, die eine klare Priorisierung bei Bestellungen und eine Warensteuerung aus Konzernsicht ermöglicht“, sagt der Logistik-Chef im Hinblick auf die Bestandsoptimierung.
Die Tochtergesellschaften platzieren ihre Bestellungen jetzt bei der „Headquarter-Ebene“. Diese priorisiert die Aufträge und steuert die Orders – und zwar auf Basis transparenter Bestände im Bestandsmanagement. Ein wichtiger Beitrag zu einer langfristigen Bestandsoptimierung. Bestandsführendes System ist das von AEB gelieferte Warehouse Management System (WMS), das mit dem ERP-System synchronisiert wird.
Auch die Bestände in den von Dienstleistern bewirtschafteten Zentrallägern werden regelmäßig im WMS abgeglichen und summarisch an das ERP-System übermittelt, so dass auf Konzernebene vollständige Bestandstransparenz im Bestandsmanagement erreicht werden konnte.
Um über die reinen Lagerbestände hinaus vollständige Auftrags- und Bestandstransparenz im Bestandsmanagement zu bekommen, müssen die Bohle-Logistiker zudem diejenigen Bestände verfolgen, die in der Luft, auf Schiffen, der Straße oder der Schiene transportiert werden.
Das ist keine zu vernachlässigende Größenordnung. Mehr als 100 Container mit Schwalbe-Fahrradreifen sind ständig unterwegs: von der Produktion in die Zentralläger in Asien zur Zentrale in Reichshof, zu den Lägern der drei Tochterunternehmen Schwalbe Nederland, Schwalbe UK und Schwalbe North America oder als Direktlieferungen ab Zentrallager an Kunden.
Auch hierbei greift Bohle auf Software von AEB
zurück: Die Software des Stuttgarter IT-Unternehmens speist sich
aus Statusinformationen, die sowohl von den Lagerlogistik-Dienstleistern als
auch den Frachtführern elektronisch zur Verfügung gestellt werden.
Außerdem werden auch Planungs- und Ist-Daten zum Auftragsstatus, z.B. Auftragseingang, Kommissionier- und Versandstatus, für das Bestandsmanagement und die Auftragsverfolgung gewonnen. Die Bohle-Logistiker bekommen dadurch ein noch genaueres Bild über den Auftragsfortschritt und wo sich die Ware gerade befindet. Für die Bestandsoptimierung sind diese Daten ebenso sehr wertvoll.
Von dieser Lösung sollen zukünftig auch die Bohle-Kunden profitieren. Unter dem Namen SCHWALBE Tire - Tracker wird dann den Bohle Kunden ein bisher im Reifengeschäft einzigartiger Service angeboten. Bei allen Sendungen, die von Asien oder von Reichshof aus direkt an Großhändler, OEM oder Einzelhändler gehen, kann der Kunde sehen, wo sich die Ware aktuell befindet und wann sie geliefert wird.
Doch die Rolle des Warehouse Management Systems als ein sehr wichtiger Bestandteil der weltweiten Supply Chain von Bohle ist nur eine Seite der Medaille. Auch in der täglichen Lagerpraxis in Reichshof-Wehnrath bewährt sich das WMS aus dem Hause AEB. Im Rahmen der Bestandsoptimierung führten die Verantwortlichen um Global Warehouse Manager Maik Kuttig und Lagerleiter Klaus Ludwig auf Basis der Auftragsdaten auch eine ABC-Analyse und XYZ-Analyse durch.
Bei der ABC-Analyse wurden die Bestände je nach Umschlaghäufigkeit in drei Kategorien klassifiziert. Die XYZ-Analyse sortierte die Bestände nach Bedarfsschwankungen über das Jahr. Das Ziel war eine Optimierung der Wege im Lager als Grundvoraussetzung für hohe Effizienz in den Lagerprozessen.
Gemäß der Klassifizierung ordnet das WMS eingehende Ware einem Lagerplatz zu. Ausgelagert wird wahlweise pickzahloptimiert, lagerplatzabbauend oder nach dem Prinzip First in – First out. Die Entscheidung trifft die Lagerleitung anhand von Kapazitäts- und Lagerplatzauslastung. Hierbei handelt es such um wertvolle Daten für das gesamte Bestandsmanagement und die Bestandsoptimierung.
Das Logistikzentrum Reichshof-Wehnrath verfügt über sechs Kommissionierplätze, an denen jeweils zwei Mitarbeiter pro Schicht arbeiten. Das System berechnet, welches Team den kürzesten Weg zur Ware hat.
Unterstützt werden die Kommissionierer durch moderne mobile Datengeräte im Smartphone-Look. ”Die Mitarbeiter mögen die modernen Oberflächen und das Arbeiten mit Apps. Das kennen sie ja auch aus dem privaten Bereich”, sagt Lagerleiter Klaus Ludwig.
Nach der Herstellung der Reifen in den Werken in Asien werden die Reifen verpackt und es wird auf Gebindeebene ein individueller Barcode pro Packstücke generiert. Neu eingeführte Prozessschritte im Bestandsmanagement sorgen dafür, dass dieser Masterbarcode die Ware über die gesamte Logistikkette begleitet. Damit will Bohle die Nachverfolgbarkeit der Sendungen als Basis für das Qualitätsmanagement sicherstellen.
Als Grundlage für die Nachverfolgbarkeit werden bereits während der Produktion in Asien die Reifen mit einem Single-Barcode versehen, der alle produktionsbasierten Daten enthält. Diese Einzelbarcodes werden bei der Verpackung in Gebinde unter einem Masterbarcode gebündelt. Schnittstellen sorgen dafür, dass auch die Informationen zusammengeführt werden können - für Bohle ist es dadurch jederzeit ersichtlich, welcher direkte Kunde welche Reifen bekommen hat.
Bei der Kommissionierung wird jeder Masterbarcode, den ein Kunde erhält, vom WMS automatisch oder durch erneutes Scannen ermittelt. Für jedes Gebinde gibt es einen klaren Übergang. „Wir haben gemeinsam mit AEB eine Lösung geschaffen, die erheblich zu einer Optimierung der gesamten Supply Chain beiträgt und strukturiertes Arbeiten im Tagesgeschäft ermöglicht“, sagt Maik Kuttig, der als Projektleiter bei Bohle für die Implementierung der Logistiksoftware zuständig war.
Lieferketten detailliert planen und überwachen. Störungen schneller erkennen und proaktiv handeln. Einfach und kurzfristig realisieren mit Monitoring & Alerting von AEB.
Für den Erfolg des Projekts floss in der Projektphase bei allen Beteiligten einiger Schweiß. ”Ein ERP-System und ein WMS gleichzeitig zu einem Stichtag auszutauschen, ist so, wie eine Herz- und eine Lungentransplantation gleichzeitig durchzuführen”, bringt Global Warehouse Manager Maik Kuttig die Herausforderung auf den Punkt.
Ein wesentlicher Erfolgsfaktor des Projekts: Die enge Kopplung von ERP-System und WMS sowie der Logistik-IT der Zentrallagerbetreiber mit insgesamt mehr als acht kommunizierenden Systemen und eng abgestimmter Prozesslogik an den Nahtstellen. Sie forderte Bohle-Mitarbeitern, Beratern und Entwicklern in der Einführungsphase aber auch alles ab.
"Priorität hatte nicht nur die Inbetriebnahme der Einzelprozesse. Genauso wichtig war bei allen Beteiligten das Verständnis für das Zusammenspiel der einzelnen Komponenten. Nur damit lassen sich Prozessschritte und Datenflüsse vollständig harmonisieren. Das galt auch für alle wesentlichen Sonderprozesse und Fehlerfälle", erläutert AEB-Projektleiter Dr. Jochen Fuhrmann.
Erschwerend hinzu kam, dass gerade die Einführung des WMS unter erheblichem Zeitdruck stattfand. ”Normalerweise arbeitet Bohle bei IT-Projekten klassisch. Wir erstellen ein Pflichtenheft, das der IT-Dienstleister strukturiert abarbeitet”, sagt Kuttig. Doch dafür fehlte diesmal die Zeit.
In Abstimmung mit Dr. Fuhrmann entschied sich das Bohle-Projektteam für ein agiles Vorgehen. Die AEB-Projektentwickler um Moritz Jung und Till Protzek konzentrierten sich zunächst auf die Hauptprozesse, die sie in mehreren Sprints programmierten. „Der Vorteil beim agilen Vorgehen ist, dass die echten Probleme früher im Projekt hochkommen, als es bei einem klassischen Projekt der Fall ist“, sagt Moritz Jung.
Nach jedem Sprint wird das Ergebnis zusammen mit den Nutzern getestet – und falls notwendig angepasst. Bei den meisten klassischen Projekten dagegen kommen die Nutzer erst in der Endphase mit der Lösung in Berührung. Der Vergleich zwischen klassischem und agilem Vorgehen fällt Nadja Rosa aus dem Bohle-Projektteam dennoch nicht leicht. Ihr Fazit: ”Man kommt mit dem agilen Vorgehen relativ schnell zu Ergebnissen. Es muss einem aber klar sein, dass später noch vieles nachgearbeitet werden muss.”
Zum Jahreswechsel 2017/2018 wurden die alten Systeme abgeschaltet und die neue IT hochgefahren – das Projekt war exakt im Zeitplan. Was folgte, war ein intensives Finetuning, das der hohen Komplexität des Gesamtprojektes geschuldet war. ”Diese kritische Phase haben wir dank des außergewöhnlichen Engagements der beteiligten Teams gemeistert”, erinnert sich Bösinghaus. Dabei schließt er auch das AEB-Projektteam ein, das mit hoher Vor-Ort Präsenz wirkungsvoll unterstützte.
Mittlerweile läuft der gesamte Prozess – und die erwünschten Aspekte stellen sich nicht nur in Sachen Bestandsmanagement und Bestandsoptimierung ein. „Die neuen Strukturen zeigen Wirkung. Wir können vorausschauender und gezielter produzieren. Und wir schaffen für unsere Kunden eine bessere Lieferperformance und einen besseren Lieferservice”, zieht der Logistik-Chef ein positives Fazit.