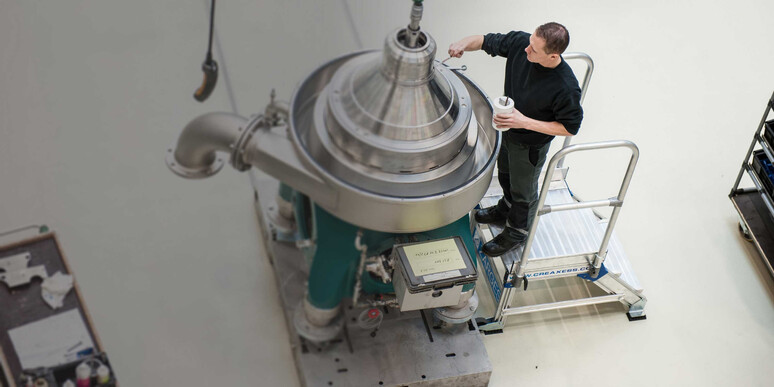
Clearly separate: GEA optimize global freight shipping
GEA Westfalia Separator Group uses AEB software for shipping and monitoring of new equipment and replacement parts – and identified even more potential to optimize freight processes.
GEA Westfalia Separator Group uses AEB software for shipping and monitoring of new equipment and replacement parts – and identified even more potential to optimize freight processes.
Clearly separate: distinguished products and streamlined shipping
Complex supply chain management for new equipment
In-house management of global parts logistics
Hosted shipping solution – cheaper and easier
Lower freight rates, better customer service
Bundling and harmonization deliver even better processes
The clientele of GEA Westfalia Separator Group consists mainly of breweries, dairies, and industrial businesses in the maritime, energy, oil & gas, chemical, pharmaceutical, renewable raw materials, and environmental technology sectors. Separators and decanters use centrifugal separation technology to separate liquids from each other or solids from liquids. Large separators are used on ships and oil platforms to clean water and oil, in breweries to clarify beer, and in dairies to separate bacteria from milk or fat from skim milk. The headquarters of GEA Westfalia Separator Group which is part of the mechanical engineering GEA Group, is located in Oelde, Germany – 70 km northeast of Dortmund. A second German plant is located in Niederahr, and there are also plants in France, India, and China.
The company receives orders for thousands of pieces of new equipment each year. The Commercial Order Processing department in Oelde centrally manages all logistics – including for the Niederahr site. Transportation is handled by a logistics service provider whose employees have been using the AEB global trade and logistics software suite since the spring of 2014. “AEB’s Shipping was already in use at other GEA business units, so we had an internal referral,” says Ulrich Tyrell, Head of Commercial Order Processing for new equipment. “We were also familiar with AEB’s Compliance Screening and Export Filing solutions, which have been used throughout GEA since 2006 and 2009, respectively.
In the spring of 2013, we made the decision to use AEB solutions for both new equipment logistics and to manage our global parts business.” Dieter Lauer, Head of Foreign Trade Department, adds: “For over ten years, we had been using a custom-programmed version of the Transport module in SAP®, but it was old and simply no longer state of the art. There was only a single connection to UPS – also custom-programmed in SAP®. We felt it was important to establish a clear separation between our SAP® system and the logistics system used by the logistics service provider. We also wanted to cut our own system administration costs.” Today, some 13 employees – at the logistics service provider and in the Foreign Trade department run by Dieter Lauer – work with the AEB global trade and logistics software suite.
The volume of shipments of new equipment is not very high, but the logistics are quite complex. Some 1,500 shipments go out each year, about 90% of them to customers outside of Germany. Individual separators, which can range in diameter from half a meter to two meters, are manufactured in Oelde and shipped directly to customers. More complex are the orders in which individual parts such as centrifuges are first shipped to equipment manufacturers in Finland, Norway, or England. These manufacturers then assemble the complete systems – including all tubes, valves, and measuring gauges – and ship them as a unit. Before, the manufacturers would e-mail the Order Processing department with information such as weight and dimensions when the system was complete.
Today, the packing data can be collected online directly in AEB’s Shipping, so GEA employees no longer need to enter it manually. “This saves time and eliminates a potential source of errors,” says Tyrell. Shipping these systems generally involves very large packages and may even require special transports with police escort. The logistical challenges in such cases are great, with packages up to 15 meters in length transported first by truck to the shipping port, then by ocean freight to destinations throughout the world. It is not uncommon for GEA to have to arrange the final leg of transport to a construction site in the most remote corners of the Earth.
While GEA employees process orders and manage shipments of new equipment centrally in Oelde, the logistics service provider is responsible for organizing transports. The company manages worldwide logistics for its replacement parts business entirely on its own, however – also from its central base in Oelde. GEA made a strategic decision to reorganize its parts supply chain. This strategy led to the 2012 opening of the European Parts and Logistics Center (EPLC) in Cologne, which now supplies all customers throughout the world except for Asia and Australia. The EPLC houses some 21,000 replacement parts – from 5 mm washers to machinery parts weighing hundreds of kilograms. This made it possible to reduce the amount of stock held on site at the subsidiaries and accelerate the availability of parts.
To more readily serve the Asian market, the decision was made in 2013 to open the Asian Parts and Logistics Center in Singapore. DHL runs the facility, but the plan from the outset was to work with Shipping from AEB. “The timeline was tight. The software was implemented within four months. The go-live was scheduled for the beginning of February 2014 – and we were ready on time,” says Dieter Lauer. Members of staff of AEB’s Singapore office trained the employees of GEA, who then passed their knowledge along to the DHL staff. “Not a single shipment has been held up since then – everything runs smoothly,” says Lauer. And that despite the fact that order processing and operations take place on two different continents – since customer inquiries from Singapore, Indonesia, Malaysia, Thailand, Australia, New Zealand, and Japan are initially received by the employees in Oelde. If the goods are available at the Singapore hub, the order is processed and the shipping data is passed to AEB Shipping. The pending shipment then appears in the worklist of the DHL employee in Singapore. Once the goods have been picked and packed, the correct labels and documents are automatically generated and added to the package, along with the packing list and invoice.
Björn Balsat, the project manager for AEB, was in Singapore for several days. Together with the colleagues from AEB (Asia Pacific) Pte Ltd, he provided support during the implementation phase: “I found the project interesting, because we were able to show how adaptable our software is. Parts shipments are fastmoving, high-volume items. The software supports the staff here with standardized processes that seldom vary. With new equipment, on the other hand, the lead times are long, and GEA must deal with very complex customer-specific demands. Many of the features that come in the standard package, such as letter of credit processing, were also well received. The employees appreciate how the software simplifies the processes.”
In introducing AEB’s Shipping, GEA Westfalia Separator Group established a clear separation between its ERP system and the logistics system. This also yielded better data quality, says Ulrich Tyrell. He is happy that the global trade processes are so stable and secure today: “Since AEB’s Shipping is hosted in AEB’s own data center, we are always accessing the latest regulations, and our IT department no longer has to worry about performing maintenance or installing updates.” Dieter Lauer remembers how it was before: “In SAP®, export documents were always generated in different places. My colleagues always had to locate and collect the various documents, then use the invoice to access Export Filing.
Now, they just hit Print and know that all the necessary export documents will be generated. The system is so easy that even the boss can understand it,” he adds with a wink. Even when new people join the team or help out temporarily to cover someone on vacation, the software practically takes them by the hand. Plausibility routines prevent incorrect data from being sent to the customs office. And Dieter Lauer got IT’s backing when it came to the software investment: “Our IT department felt it made both business and financial sense to have the system hosted by AEB.”
The AEB solution supports GEA Westfalia Separator Group with Freight Cost Management and Transport & Freight preparation as well. “We have much greater ease of use than before,” reports Dieter Lauer, Head of Foreign Trade Department. Now the staff has IT support in sending out early notifications and reserving carrier capacities. The planning leeway is greater, explains Lauer, and emphasizes: “This is especially important toward the end of the year, when we have large shipments coming up and want to be sure we book the necessary cargo space. We confirm the cargo space as soon as we have the packaging data and precise shipping dates. The option of bundling shipments lets us take advantage of cheaper freight rates. We still have a lot of potential to save freight costs here in the future.”
The introduction of AEB’s Supply Chain Collaboration platform was also a big step forward in improved quality of service. The new platform succeeded in bringing transparency to the entire supply chain. The Monitoring & Alerting solution lets customers check the status of their own orders at any time. Customers who order equipment receive an e-mail with a link, just as we’ve come to expect with anything we order online. Clicking the link brings them to AEB’s Monitoring & Alerting, where they can track the progress of their orders. Customers also have access to documents directly in Monitoring & Alerting – such as consignment papers and Shipping documents, which they can download and print out themselves to accelerate customs clearance, for example.
Not many companies offer this service, says Ulrich Tyrell with pride. The common practice is still to send the customer such documents by e-mail or fax. And GEA intends to make its logistics even more service-oriented. The company is in the process of expanding the visibility of milestones in Monitoring & Alerting. Starting in 2015, customers should be able to see exactly when the company sent out the goods, when they were loaded onto the ship, when the ship left port and arrived at its destination, and when the goods were handed over to the carrier.
AEB software is also helping to provide greater legal protection. Since 2006, all business units of the GEA Group worldwide have used AEB’s Compliance Screening software to run automatic restricted party screening. GEA plans to roll out the Export Controls solution throughout the company in 2015, making it easier to identify which exports require a license. And Ulrich Tyrell has even more improvements in mind, such as a further harmonization of logistics.
“There are enough Shipping processes that could still be further optimized. We could save even more by consolidating our shipments to business partners in Norway, Finland, and the UK, for example.” The Head of Commercial Order Processing sees a significant potential for even more savings if functionalities such as auto-assign, which automatically groups shipments, were better used. This would require taking an even closer look at the logistical processes. The software is driving this line of thinking. Tyrell sums it up: “AEB software solutions help us find the potential for optimization and further harmonize our logistical processes.”