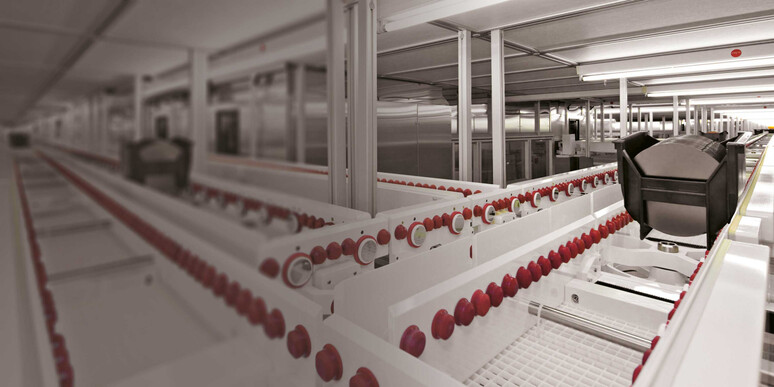
Infineon: Efficient freight control and shipping of wafers & chips
Infineon sends out 1.5 million shipments of wafers and chips a year from Europe, Asia, and the US – processed smoothly and without errors by AEB shipping and freight software.
Infineon sends out 1.5 million shipments of wafers and chips a year from Europe, Asia, and the US – processed smoothly and without errors by AEB shipping and freight software.
Moving pizza boxes around the globe
From Villach via Malacca and Singapore to Tokyo
The role of shipping software in transport logistics
Fewer returns thanks to IT monitoring of shipments
Flexible shipping software allows customizations
Shipping support across multiple time zones
Shipping solution in the new China distribution center
Coming soon: AEB solutions bring transparency to freight costs
From the outside, they look like normal pizza boxes. But open them up and, instead of pepperoni or sausage, you’ll find rolls of a thousand or so high-tech microchips packaged in clear plastic foil. Infineon sends out about 15,000 of these pizza boxes each day from its production facility in Malacca, Malaysia, to its distribution center in Singapore. Malacca is Infineon’s largest production site and one of 14 sites running software solutions from AEB’s Transport & Freight Management portfolio. The company processes a total of 1.7 million delivery notes each year – corresponding to some 1.5 million outbound shipments – with its nine Transport & Freight Management systems from AEB installed around the world.
High-tech giant Infineon has used AEB software for over 16 years. Since 2001, Infineon workers in eight countries have used AEB’s Transport & Freight Management solutions to control internal shipments between production facilities and to its distribution centers as well as outbound shipments to its customers.
Fast, efficient, accurate shipments are paramount in the high-tech industry. Infineon’s customers expect no less. The chipmaker is a second-tier supplier to customers such as Bosch, Continental, Delphi, Giesecke & Devrient, HP, Nokia, Schneider Electric, Philips, and Samsung. Infineon chips drive automotive powertrains, control energy transmission in wind turbines, and protect the security of electronic identity cards, credit cards, and electronic access cards. With some €3.9 billion in revenues in 2012, Infineon is Germany’s largest semiconductor manufacturer and number two in Europe.
Infineon has established a three-stage global logistics and distribution network. Wafers – the primary material from which chips are made – are manufactured at the production facilities in Regensburg and Dresden in Germany, Villach in Austria, and Kulim in Malaysia. Afterwards, the wafers are sawed and processed into chips in the plants in Regensburg, Dresden, and Warstein in Germany; Cegled in Hungary; Batam in Indonesia; Malacca in Malaysia; and Wuxi in China. The chips are then wired at their contact points with the interconnects facing out, mounted, and stamped before the finished chips are packaged in the pizza box.
Three distribution centers (DCs) coordinate distribution to the end customers: The DC in Singapore serves the entire Asia-Pacific region, including China, Japan, Australia, and New Zealand. The United States DC in Hayward, near San Francisco, serves customers in North and South America. The European DC in Großostheim outside Aschaffenburg, Germany, handles customer orders in Germany, Scandinavia, and southern Europe.
Infineon first uses AEB’s Shipping software for its internal shipping, which involves loading the semi-finished goods into containers and shipping them from one production facility to another. All the finished products are then shipped by air to the distribution centers, where they undergo inbound checks and interim storage before being shipped to the end customers. In the distribution centers, it is the employees of the Infineon logistics service providers who use AEB’s Shipping to prepare the goods for transport. The DC in Singapore is operated by DHL, and the European and American DCs are operated by Kühne + Nagel.
Großostheim holds the record for the most packing and weighing stations running the AEB software with 40 Shipping workstations. During peak times, some 2,000 shipments are prepared here each day. The European DC was also the first Infineon site to use the AEB AEB’s Shipping software. After that, it was gradually rolled out in the Asian and US sites. “In our European DC, we process nearly 270,000 delivery notes per year. In our largest manufacturing plant in Malacca, we actually process over 450,000 delivery notes each year. That alone shows how powerful the system is,” says Rupert Herz, who is in charge of the AEB Transport & Freight Management systems at Infineon.
The introduction of AEB’s Shipping made it possible to manage the high volume of packages with stability and reliability. IT support ensures accurate, on-time customer shipments.
Herbert Helmbrecht, Senior Manager for IT Supply Chain Management, is responsible for shipping-related issues for all Infineon sites worldwide. “Before – and this was quite some time ago – it sometimes happened that the quantity was wrong or a customer received the wrong goods. Since we started using AEB’s Shipping, return logistics have decreased and the process is simpler and more streamlined, since employees can take care of everything from a single workstation,” notes Helmbrecht. “While packing, our employees check to make sure the shipment is complete and immediately print all the necessary labels and documents, which they can then insert and affix right away. This made it possible for us to greatly reduce our shipping error rate.”
Inbound checks are carried out in all three distribution centers. They ensure that goods unloaded from containers are complete and help monitor the stock put-away process. The timestamp shows when the goods where entered into stock. This also makes it possible to offer the premium service of cross-docking goods that the customer is waiting for as soon as they arrive at the distribution center, Helmbrecht explains. “The outbound check is also used to set a timestamp when the goods are issued from the DC. From this point forward, the responsibility lies with the carrier, and on-time performance is one benchmark for measuring carrier performance,” says Helmbrecht.
AEB’s Shipping automates all weighing, packing, and labeling processes to ensure accurate deliveries. The software is so flexible that it provides optimal support even for custom logistics processes, helping Infineon to further enhance the quality of its service.
About 30 percent of the company’s shipments now feature custom labels that automatically conform to customer-specific requirements. The result has been a higher quality of service and better internal processes. Take cross-docking, for example: From Cegled in Hungary, all semi- finished products are shipped to Warstein, where they are bundled with other products and sent to the next destination without ever being checked into storage.
The Shipping workstations in Cegled affix both address labels in advance: one for the internal shipment to Warstein, and one for the end recipient. The system also helps manage time-critical shipments more efficiently with tools such as the “sub-package bundle”: “To save shipping costs, we often bundle multiple large delivery notes into one shipment,” explains Herz. “For a shipment that is going to be picked up in an hour, it doesn’t do any good to put pressure on the packer to hurry.”
For such cases, AEB’s Shipping allows parallel processing of shipments. Infineon has five packers work independently to prepare the delivery notes for shipment. Whoever processes the last delivery note in the bundle can consolidate the shipment in the system and close it. “We appreciate this flexibility that the software offers. It has allowed us to refine many of our logistical processes over the past years,” says Herz.
Infineon has always had production facilities in Asia. The high-tech company used AEB’s Shipping to control shipments from its Malacca site as early as 1997, while it was still part of Siemens. In 2001, it introduced the Shipping software across the board at all its production and distribution centers. The year 2001 was also when AEB opened its branch office in Singapore. The goal was not only to expand internationally but to offer professional support to customers like Infineon spread out across several time zones.
AEB sent two of its employees to assist in the rollout of the Malacca site, and the number of employees in the offices of AEB (Asia Pacific) Ltd Pte has grown since then. Account Manager Sebastian Zilm, who coordinates all expansion projects from AEB’s end, now also works from the Singapore office. “We essentially followed AEB’s global key accounts, so we were able to provide on-site training for the Infineon workers in Malaysia, Singapore, and Wuxi. Our staff offers Infineon 24/7 support that also benefits Infineon’s workers in Europe and the United States,” says Zilm.
For IT Supply Chain Manager Herbert Helmbrecht, there is no alternative to the AEB Shipping software: “When it comes to managing shipments, we view AEB’s Transport & Freight Management as a best-of-breed solution. Right out of the box, it offers all the features we need. Now that we’ve repeatedly adapted the software to our exact needs, there is no rival product on the market today that would allow us to manage our shipments with a comparable level of quality.”
ASSIST4 System Manager Rupert Herz agrees: “When we chose AEB’s Transport & Freight Management twelve years ago, the system availability, stability, and decentralized approach were important factors. Then as now, our shipping activities were distributed across fourteen sites. Having nine independent installations made us well equipped to handle a potential system outage, so we knew we could always keep our commitments.”
And soon, another site will open in China. Infineon is currently conducting an internal study to predict how the flow of goods will evolve in the coming five years. AEB’s Shipping data is used to produce the statistics on the current volumes of deliveries and shipments. “We are already planning today for 2018, and next year we will open our new hub in Shanghai so that we can supply our Chinese customers directly,” Helmbrecht reveals.
“Linking a new site to AEB’s Shipping is relatively simple,” says Herz. “The preparatory phase – equipping the finished site with workstations and printers, training the employees, and carrying out a dry run with local sites – takes about three months. Once the software is installed at the workstations, it’s a matter of a couple of hours to configure everything to where the first delivery notes can be imported and the site can go live.”
Optimized supply chain processes from procurement to fulfillment with AEB's supply chain and logistics software. Including monitoring and alerting, carrier integration, shipping processes, freight and logistics cost management, and warehouse management at the heart of global distribution centers.
AEB’s Transport & Freight Management has the potential to cover not only a wider regional scope but also a broader functional spectrum at Infineon. “We have plans for the near future to begin using AEB solutions for Freight Cost Management including self- billing as well,” says Helmbrecht, who is confident this step will bring greater efficiency and cost savings. Currently, freight cost calculations are managed in complex Excel spreadsheets or left to external service providers. In the future, AEB’s Freight Cost Management will automatically calculate the amount and issue a direct credit to the transport service provider.