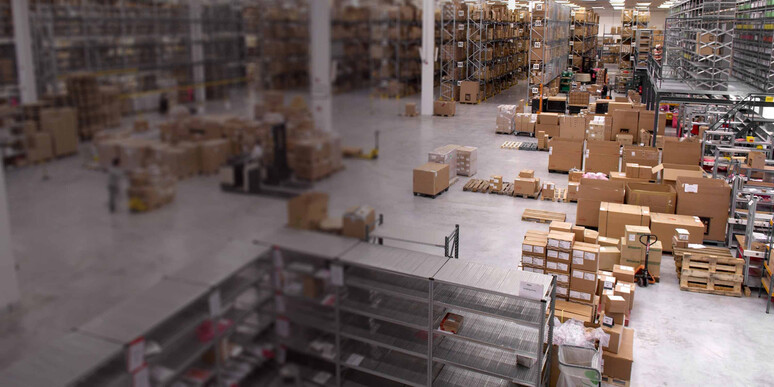
TTI: Streamlining shipping and exports with AEB software
Electronics distributor TTI automates shipping, export, compliance screening, and freight cost management with AEB software to improve distribution efficiency.
Electronics distributor TTI automates shipping, export, compliance screening, and freight cost management with AEB software to improve distribution efficiency.
As the end of the working day draws to a close in other company departments, this is often the busiest period in logistics. That is also the case in the shipping department of the distributor for electronic components and connectors TTI in Maisach-Gernlinden near Munich, Germany.
At 50 packing stations, TTI staff prepare 1,600-1,800 shipments per hour for dispatch in peak periods. It comes down to the minute - after all, the approximately 11,000 customers are highly dependent on the timely delivery of the electronic components supplied by TTI.
In addition to the experienced staff, the shipping software plays a key role in timely dispatch. "A system failure during peak times is something we cannot afford. When all hell is loose at the packing stations, the software must not be a bottleneck," says Martin Brennecke, Director of Information Services at TTI in Europe.
In this respect, it was a highly sensitive IT project that TTI opted for in October 2014. The intention was to replace the previous, somewhat outdated shipping software with a more modern solution: the choice fell on Shipping from the Stuttgart-based software company AEB. The new Shipping solution has been running in live operation since April 2015 – to the satisfaction of Brennecke and his team. There were various reasons for the replacement: Although the previous solution had been working reliably for many years, the provider had not consistently developed it further.
The adjustments required by TTI but also the switch to 64-bit technology were accordingly complex. In addition, three different solutions were being used for shipping as well as the associated export processes and the sanctions list screening. In contrast to that, the AEB software suite combines these three applications (Shipping, Export Filing, and Compliance Screening) into one solution and accesses a common database in the process.
"That saves us a fair amount of extra manual work," says Brennecke. The Director of IT summarizes the strategic dimension of the project, "TTI earns its money with the warehouse. Therefore, we needed a sustainable solution for shipping including export and screening that can be quickly adapted to changes in our business processes and where the software supplier guarantees long-term support."
The demands were high – Alois Fruth, Project Manager at AEB and his team, for example, had to be prepared for a range of project-specific challenges. That included having to embed the AEB software into the IT environment. The ERP system is an in-house development by TTI which the parent company in the US supports. Although the Warehouse Management System comes from a software provider, it was then further developed by the IT department of TTI. In order to keep the complexity low, TTI and AEB decided not to make any changes to the ERP and WMS systems. The interface to the ERP system also remained unchanged.
The second challenge: The legacy software was a system programmed in the US and developed over a 15-year period, presenting challenges for TTI in terms of software and process documentation. The project therefore began with detailed research and analysis. "The AEB team provided us with excellent support in obtaining information," praises Brennecke. The AEB experts already identified some process improvements during the analysis phase, for example, in optimizing collective customs declarations. On the basis of the analysis, the systems were set up, configured, and connected via the AEB interface as from January 2015.
An extended test phase – partly in parallel operation with the legacy system – helped to minimize errors during the actual go-live. "TTI did not stipulate a tight schedule. A smooth start was more important than fast implementation," says AEB Project Manager Fruth. In parallel to the programming tasks, 15 employees from TTI's IT and shipping departments were given comprehensive training for AEB’s software solutions.
Finally, the time for a fresh start with AEB’s software solutions arrived at TTI on April 19. During the first week after the start-up of the new software, AEB staff were permanently on location at the distribution center to enable them to intervene quickly in the event of any teething troubles. The measure proved successful. "There were no significant impacts on operations due to the changeover," says Brennecke.
"For the staff at the packing tables, every error is one too many, of course. From the IT department's point of view, we are highly satisfied with the start." Today, TTI handles an average of 5,000 consignments daily with AEB solutions. In the process, orders continue to be recorded in the ERP system and transferred to the Warehouse Management System WCS and AEB’s Shipping. WCS initiates stock removal and picking. AEB’s Shipping performs several tasks at the same time. On the basis of a freight code from the ERP system, the Carrier Connect module identifies which carrier should transport the consignment and which service agreement is to be used for the transport. With the help of this information, the software creates the shipping label and the loading papers according to the requirements of the respective transport company. This is by no means a trivial task as the different forwarders and parcel services have just as precise as nonuniform requirements with regard to the address label and routing information for the consignment.
The benefit for TTI: The company no longer has to take care of any changes to the carrier systems in the interfaces – nor of any new requirements in respect of shipping labels and documents. These are maintained by AEB and flow into the Carrier Connect solution via updates.
In addition to printing the labels and shipping papers, the AEB solution assists with Freight Cost Management calculations. The software calculates the freight costs with AEB’s Freight Cost Management on the basis of the freight agreements stored in the ERP system, as well as the dimensions and weight of the shipment, and passes them back to the ERP. For export shipments, AEB’s Shipping and Export Filing provide the shipping documents, commercial invoices, and other necessary documents required for the destination country.
Last but not least: Part of the overall solution is ensuring compliance – with AEB’s Compliance Screening. In the background, the system compares the address data with the current sanctions lists of the EU and the US. Also in this case, TTI no longer has to take care of the lists being up-to-date – AEB updates the sanctions lists immediately in the Compliance Screening software with any changes.
Six months after the start of live operation, Martin Brennecke makes a positive assessment. "The higher level of integration and the associated reduction in manual work have improved productivity in the warehouse. That applies particularly to the export processes that are becoming increasingly important for our company due to a rising number of consignments destined for export," praises Brennecke. In addition, the AEB solution is more economical in both maintenance and support than the three previous solutions.
The employees in the packing zone are also delighted about another effect: Label printing is now considerably quicker than with the old solution. That increases productivity and provides relief in peak periods before the cut-off time. Incidentally, the topic of dispatch IT has not lost its appeal either for Brennecke or for AEB. The IT Director at the distributor already has the first enhancement and adaptation requirements at the ready.