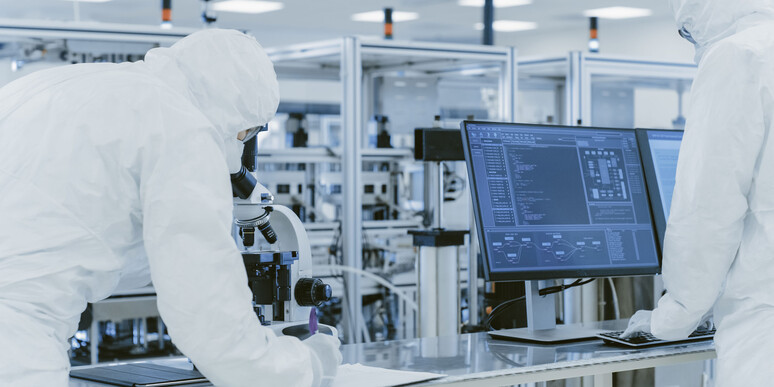
Managing carriers: Evatec's AEB connection
How the Swiss “Thin Film Powerhouse” relies on our Carrier Connect software to manage the forwarders and parcel services that reliably transport spare parts around the world.
How the Swiss “Thin Film Powerhouse” relies on our Carrier Connect software to manage the forwarders and parcel services that reliably transport spare parts around the world.
Order Processing & Export Controls Manager Denise Noser and Export & Import Specialist Stefan Hofstädter of Evatec recall the journey to perfect spare parts logistics that began in late 2014. Evatec was acquiring the Advanced Technologies Segment of Oerlikon OC, and the integration presented new challenges for those managing outbound logistics.
At the time of the acquisition, all shipments were entered manually through the individual online portals of the various parcel services. When Evatec wanted to ship a package with TNT, for example, an employee had to feed the consignment data into the TNT portal. If FedEx was handling the transport, then the data needed to be input through the FedEx portal.
Before the acquisition, this was doable. But as growing business led to more transports, the workers could barely keep up. The process was not compatible with how parts orders were managed: It took far too much time, and the resulting crunch led to errors. In one instance, an order of parts was mistakenly shipped to China instead of the United States. “You can imagine how much trouble it was to get the parts back and redirect them to the proper recipient,” Hofstädter recalls.
Spare parts logistics has taken its place alongside Evatec’s platform projects as a key pillar of the company’s operations. Over 600 packages of spare parts are shipped via forwarder or parcel service to customers each month. The company is a specialist in the development, production, and distribution of high-tech thin film deposition systems for the semiconductor, optical, and optoelectronic markets. Evatec AG has main offices in Trübbach, Switzerland, with branch offices in Germany, North America, Singapore, Malaysia, China, and Taiwan. Evatec’s customers are spread around the globe, and its spare parts shipments are usually time-sensitive.
It quickly became clear that something had to change. One provider and one smart software solution: That’s what was needed to bring order to Evatec’s spare parts logistics. Communications with transport service providers had to be drastically streamlined. Evatec had reached out to one vendor, but their proposal was not convincing: too high a price with too little service.
After an appropriate evaluation process, the company decided to go with AEB and its Carrier Connect product, which offered a solution for easily integrating forwarders and parcel services into Evatec’s internal processes. All that was needed was an interface from Carrier Connect to the materials management system already in use at Evatec.
But there was a catch: Evatec uses its own operating system, BPS, which made the task of programming an interface more complicated. For the initial phase, AEB responded with a quick and easy transitional solution that had employees input consignment data manually into the AEB software. “That was not yet an ideal solution, but it did allow Evatec to work with just one system instead of several different systems,” notes Anastasia Riedel, Project Manager for Evatec at AEB’s Zurich office.
For Denise Noser and Stefan Hofstädter, the transitional solution was a challenge, but they did see an upside: “Now we are intimately familiar with the AEB software and can troubleshoot any problem that may arise.”
The second phase involved creating an interface to the proprietary BPS operating system to replace the transitional solution. It took lots of back-and-forth between AEB and the developers until the interface between Carrier Connect and BPS was in place. But AEB also gained something from its efforts: “We used this experience as an opportunity to further refine our instructions for external parties,” confirms Riedel.
The interfaces have been up and running since May 2017. Now, the AEB solution just runs in the background and does not need to be opened separately. Noser and Hofstädter are happy with the product: “The system is always running.” AEB works in the background to maintain the interface and install regular updates of the carrier data. It’s important, after all, to ensure that the customer is always able to fulfill its shipping orders. “We need a reliable system running in the background to support our parts shipments. Our customers around the world expect prompt, perfect service,” adds Noser.
The new setup guarantees good performance in spare parts logistics at all times. Month for month, Evatec sends out more than 600 packages of parts from its main offices in Switzerland – four times the volume before the acquisition. The electronic links to FedEx, TNT, DHL, and UPS are in place, and more spare parts logistics providers have been added. “We realize, of course, that our customers may sometimes stop doing business with one provider or another. When this happens, the workflow with the new provider needs to be in place. With Carrier Connect, switching over is no problem at all,” assures Riedel.
All the shipping orders are captured in Evatec’s BPS system and packed in the company’s goods issue area. Workers there only need to add the weight and consignment size, then the system generates the label and export papers. Dispatchers just retrieve the label and papers from the printer, and the shipment is ready to go. AEB adapted Carrier Connect to also work with a laser printer, which Evatec preferred over the standard thermal printer. Now, shipping labels are generated for both printer types. “This benefits other customers as well,” Riedel notes.
Labels vary from one carrier to another, of course. A printer generates the appropriate label – along with the specific ID numbers and routing data – for whichever provider is responsible for the transport. There are four labels for FedEx, UPS, DHL, and TNT – plus a fifth label for all orders sent through a forwarder. At the end of each workday, one click is all it takes for the software to generate a manifest for each provider. The driver then confirms acceptance of the consignments.
The spare parts logistics processes that now run seamlessly at Evatec are still a source of frustration for export and supply chain specialists elsewhere. “In many other companies, the process of entering orders, transmitting consignment data to transport service providers, printing labels, and sending out shipments is still not adequately integrated and automated. This means lots of manual work and unnecessary mistakes,” emphasizes Riedel. “Carrier Connect is the solution to these problems that are so common in parts logistics.”
Seamlessly integrate all your forwarders and parcel services into your workflows through a single digital platform. This streamlines your shipping processes and makes it easier to collaborate with your transport service providers. And if you do need to switch providers, it takes just a few minutes.