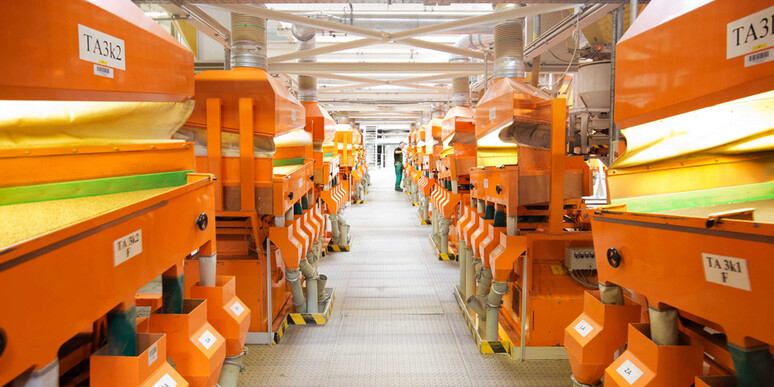
KWS transport and carrier management: a bountiful harvest
Seed specialist KWS increases competitiveness through supply chain digitization and transport optimization. A new carrier management portal from AEB takes efficiency to new heights.
Seed specialist KWS increases competitiveness through supply chain digitization and transport optimization. A new carrier management portal from AEB takes efficiency to new heights.
The digitization of transport logistics is still an elusive dream for many companies. But KWS – a seed specialist based in the northern German town of Einbeck – has largely turned this dream into a reality in the past year. Head of Logistics Andreas Römmert and his team set up a carrier management portal (CMP) that achieved several objectives simultaneously:
It automated the process of assigning orders to carriers, monitoring transports, and generating alerts when delays occur – and it enhanced the efficiency of the transport chain as a whole. The data gathered through this platform also allowed KWS supply chain managers to improve performance and laid the groundwork for further optimization. For Römmert, it’s a win-win: “The expense of setting up the CMP already paid for itself in the first year.”
That’s good news for the entire KWS Group. “We need to be sure that our seeds will reach our customers quickly. Good supply chain performance is a key factor in our customers’ purchasing decisions,” adds Michael Spellerberg, Assistant Head of Logistics at KWS, emphasizing the importance of efficiency.
Making customers happy is no mean feat. First of all, because KWS seeds are in demand throughout Europe and around the world. But also because the supply chain varies greatly depending on the type of seed. An example: KWS is the global market leader for sugarbeet seeds. Growers produce the seed base, then transport it to Einbeck to be prepped, cleaned, and pelleted. From this central hub in Einbeck, KWS then sends sugarbeet seeds to all its customers around the world.
The supply chain for corn seeds is completely different. Corn seed production in Europe is decentralized and distributed to customers from multiple sites. Corporate Logistics in Einbeck is responsible for organizing European-wide transports, but the various sites manage their own regional transports.
The differentiated supply chains weren’t the only challenge facing the logistics professionals at KWS. The diversified system environment also posed a problem, with customer orders coming in through the SAP® system, the warehouse management system of the growers, an online dealer portal, and even manually. Previously, none of this was ever consolidated into transport orders in one centralized system, and there was never a single IT-based system for communicating with the carriers. With one exception: DSV, the forwarder that handles the greatest volume, was connected to the SAP® system through an EDI link. Even before the CMP was rolled out, DSV received orders and reported back shipping statuses electronically. For the many other carriers, however, this type of complex direct link was out of the question.
Römmert hoped a new setup would automate communications with the carriers and, with the help of valid performance indicators, improve transparency in the supply chain. Previously, when a customer asked about the shipping status, KWS had to call the carriers or use their tracking systems. The solution that KWS envisioned was to establish a carrier management portal that would consolidate and harmonize the data flows between the KWS systems and the various carriers.
After a long conceptual phase, Römmert and his team put out a request for proposals. AEB submitted the winning proposal. The software company, a logistics specialist, proposed establishing the CMP based on the solutions AEB Supply Chain Collaboration and AEB Transport & Freight Management. “We decided to go with AEB for a number of reasons,” explains Römmert. “First, we had already had good experiences with AEB solutions in the past. Second, the solution met our requirements and also included a feature for printing out parcel service labels from within the system.” The versatility of the solution was a plus for Römmert: All the necessary features in a single system, including interaction with other AEB products for functions such as compliance and customs management.
Optimized supply chain processes from procurement to fulfillment with AEB's supply chain and logistics software. Including monitoring and alerting, carrier integration, shipping processes, freight and logistics cost management, and warehouse management at the heart of global distribution centers.
Once the decision had been made, the work to set up the CMP could proceed. AEB worked closely with the in-house IT department at KWS to connect their internal front-end systems and the systems of the carriers. This meant overcoming technical challenges and also convincing the carriers to allow the linkage with their systems. AEB succeeded on both fronts, and the flow of information between KWS and its carriers is now largely automated and synchronized with the flow of goods through AEB's Carrier Connect. Transport orders are sent from the CMP to the various carriers. The carriers must then pick up the goods within the agreed dispatch window.
Once the pickup has occurred, the transporter sends a status update to the CMP. If no pickup is reported before the dispatch window closes, the CMP automatically generates a warning to the carrier’s dispatcher and to KWS. Each side then has time to clarify the reason for the delayed pickup and initiate the proper response early enough to ensure that the shipment reaches the customer on time.
The customer also receives an automated notification with the time of delivery. Once the goods have been successfully delivered to the customer, the carrier issues a delivery confirmation. If no delivery confirmation has been received by the promised delivery time, the CMP automatically generates a late delivery alert to both KWS and the carrier’s dispatcher.
Römmert and Spellerberg feel that this arrangement benefits their company greatly. “We have standardized and optimized our transport processes, eliminating any hiccups between our in-house systems,” says Römmert with satisfaction. Spellerberg points out that comprehensive tracking & tracing of both forwarders and parcel services has greatly enhanced transparency in the international supply chain. “We can measure dispatch and transport times for any carrier to ensure they’re complying with the terms of our agreements,” Spellerberg explains. The CMP data provides an objective basis for doing so.
KWS is also using the data to establish transport-related key performance indicators (KPIs) as a basis for a continuous improvement process (CIP). Plans are now underway to use the KPIs to establish a system of bonuses and penalties for on-time performance in pickup and delivery. KWS is already the benchmark among its customers for its lead times. Another benefit: The delivery confirmations can be used to document the receipt of shipments outside the EU for VAT purposes. But did the project make financial sense? Definitely, say Andreas Römmert: “We amortized the costs within just one year.” The electronic link to the carriers did more than just lower the costs of managing transport processes. IT costs are also down.
“Interfaces cost a lot of money. Focusing on a single interface to AEB greatly streamlines our operations.” AEB is responsible for maintaining the interfaces from the CMP to the various forwarders and parcel services. But KWS is not content to rest on its laurels. The company plans to integrate additional features, introduce a system of bonuses and penalties, and roll out the solution internationally. The KWS slogan “Seeding the Future” also applies to the company’s international transport logistics.